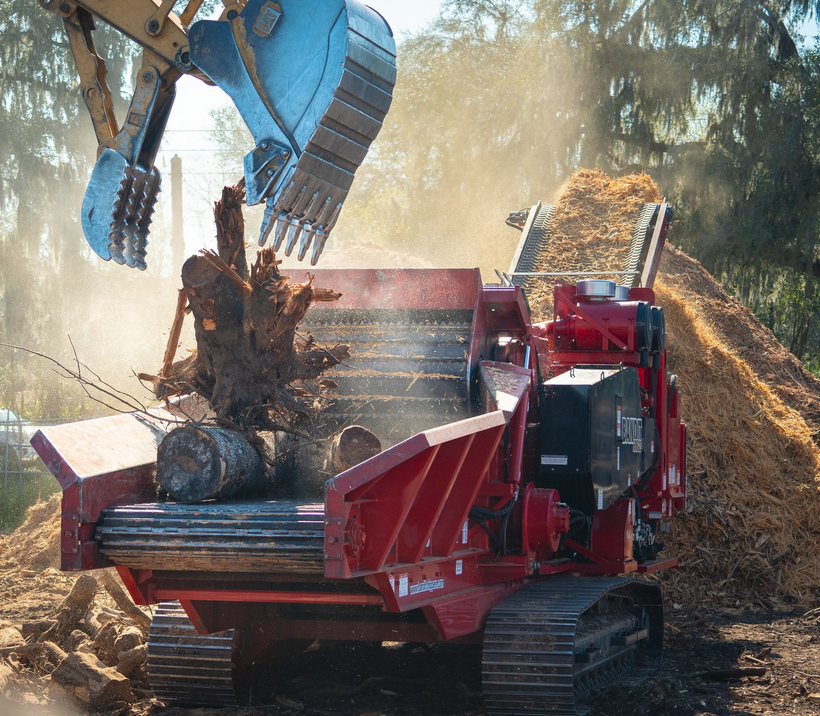
The heart of the HM6420 is a 50” diameter x 66” wide hammermill. The heavy-duty mill features a 1.75” drum skin custom formed from rolled plate. The mill is supported by a 7” main shaft constructed of alloy steel that has been ultrasonic tested. Each pocket within the mill is manufactured from high strength A-514 steel. These combinations create a structural sound mill for added durability and integrity. The mill is equipped with 20 carbide infused hammer inserts built to withstand the toughest material fed into the machine. Each holder is securely attached to the mill via a patent-pending quick change pocket system. Each holder recesses into the mill pocket, increasing durability. A top plate covers the pocket and holds in place by six hex bolts. The hammer insert is attached to each holder utilizing two bolts. With this set-up, the mill hardware is easier and quicker to replace.
A heavy-duty slat-style infeed conveyor is directly driven generating over 18,000 pounds of pulling power. The large diameter feed wheel is also directly driven and provides an additional 17,000 pounds of pulling power and 8,650 to 17,300 pounds of down force when hydraulic pressure is applied. These combinations allow the HM6420 to grind massive quantities of material efficiently and effectively at one time.
A proportional feed system is standard and regulates the feed system from 82 – 132 feet per minute.
The HM6420 has one of the fastest feed rates on the market allowing it to quickly process material. The proportional feed system allows operators to adjust the feed based on material being processed ensuring maximum output and grinder efficiency, all while achieving a higher quality end-product.
Three screens are located on the top side of the HM6420 mill. A variety of screen sizes are available up to 10” to produce various end-product sizes. The top feed wheel moves upward, and a removable screen cradle allows for quick screen set-up changes. All work for screen changing is performed outside of the machine.
An impact detection system is standard and designed to limit damage if a contaminant is struck inside the grinding chamber. Once an impact event is detected, the grinder will idle down, open the gate, disengage the clutch, and reverse the feed.
Key Features
• 50″ diameter x 66″ wide mill with 20 inserts
• 1,200 hp Caterpillar diesel engine
• 16′ long x 64″ wide steel infeed conveyor
• Radio remote control with tether backup
• 6-speed proportional infeed conveyor (82 – 132 FPM)
• 37.75″ diameter floating feed wheel (8,650 – 17,300 pounds of down pressure available)
• 56″ wide discharge conveyor with 16′ 8″ stacking height
• Three easily replaceable screens